
The Engineering department at Sacred Heart University created an electronics kit that included the necessary equipment to conduct their classes. The issue was there was a lack of storage in the space for them. Originally, I was tasked with creating a shelf to store them, but we soon realized that the boxes on the bottom would be too difficult to reach on a regular basis. My team and I settled on a pull-out drawer. I designed a drawer to hold all 16 kits as well as have room below to store two large containers with extra supplies.
After some measurements and evaluations, I was able to drill in place the rails which are rated to handle up to one hundred pounds when fully extended. This was necessary because of the weight of the drawer itself was constructed out of ¾ inch plywood.
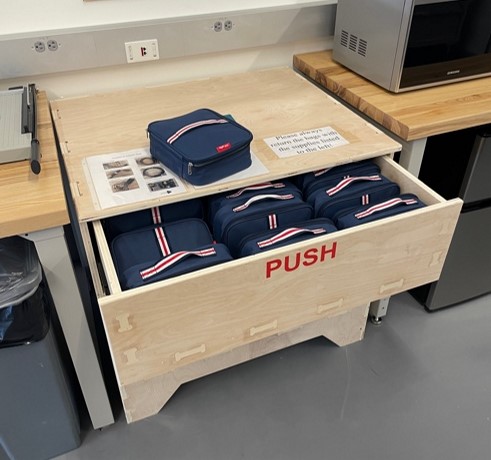
My main problem with the drawer was a miscalculation of the placement as the rails have a push-to-open mechanism. When pushed incorrectly the drawer would not open making it difficult to open the drawer. After moving the rails and cutting back some of the panels, I made the drawer flush, thus making it a press to open.